
Sustainability Features
Building Enclosure
CONSTRUCTION
Throughout the design and construction of the project, the owner and design team made every effort to utilize their full strength through collaboration. This effort necessitated a unique delivery method for the project called Single Selection Method. According to Chapter 193, Section 21B of “An Act Further Regulating Public Construction in the Commonwealth”, this method is defined as follows: “The method or process by which a designer and a construction management at risk firm submit jointly as a team in response to a request for qualifications and proposals and are evaluated and scored as such by the authority.” In other words, ADD Inc and Suffolk Construction submit together as a team and receive separate contracts from the Massachusetts State Building Authority. This method is closely related to CM-at-Risk.
The success of this delivery method is seen clearly in the cost of the project, the dates of construction, and the overall quality of design. Completed in just 2 years, this LEED Gold certified high rise remained under budget with a total project cost of $64.3 million. Project budget was a key concern during design because the owner receives no appropriation from the Commonwealth of Massachusetts. Therefore all revenues to support the construction of university facilities are derived from the rents and fees paid by students.
ELECTRICAL
The Tree House operates on secondary service power, meaning that the power company owns the transformer which supplies power to the building. This type of set-up is typical for the area. HVAC equipment on the roof level and in the basement receive power from two switchboards at 480/277V. Eight transformers step down the power to 208/120V in order to serve the lighting and receptacle loads.
A generator oil heater on automatic transfer switch supplies emergency power to the building. Only life safety loads are connected to this generator. Residential units are not on standby power. This set-up makes the generator smaller and easier to fit on the roof.
LIGHTING DESIGN
Lighting design follows the creative and sustainable ambitions woven throughout the project. Passive daylighting techniques informed much of the architecture of the façade. Small punched windows in the bedrooms are shifted toward the north wall of the room, allowing light to reflect off the wall rather than being absorbed by the floor. Large glazing panels accent the community studios and workrooms on each floor. Linear fixtures in many of the common spaces and bedrooms correspond to the linear aesthetic of the façade.
Controlled by toggle switches, the building uses a mixture of T5 and T* fluorescent light sources. Compact fluorescents and some LEDs are also used. Metal halide track lighting is also implemented to accent artwork in the lobby space. The café space on the ground floor breaks from the linear orientation seen throughout the rest of the building. Linear fixtures are placed at random orientations to provide a more eccentric atmosphere; however, this technique likely sacrifices a uniform light distribution. For the common spaces on each floor, downlights and linear sources are combined and provide significantly more light than the residential units.
MECHANICAL
Two air handling units (AHUs), one located on level 2 supplying 16500 CFM of air to levels 1-3 and one in the penthouse, supply 23200 CFM of air to levels 4-20. The penthouse AHU is coupled with two-pipe fan coil units (FCUs) in every zone from levels 4-20 that all either heat or cool simultaneously. The penthouse AHU and FCUs use chilled water supplied by two water cooled chillers with 175 tons of capacity each with a two-cell cooling tower to reject the condenser heat. The level 2 AHU has a dx coil combined with a 43.8 ton air cooled condenser. Two 2650 MBH natural gas boilers provide hot water to both AHUs and the FCUs. There are also three split air conditioner units to meet the electrical rooms cooling loads on level 2, level 3, and the penthouse with capacities of 34.2 MBH, 24 MBH and 24 MBH respectively.
STRUCTURAL
The structural system consists of a deep foundation system and steel superstructure. Steel H-piles support the foundation of the building and provide both compressive and tensile support due to overturning. Concrete grade beams and slab-on-grade also mitigate poor soil conditions. Steel framing with composite decking provides gravity support, and a combination of moment frames and concentrically braced frames resist lateral loads.
Though the footprint is small, the structure of the building is relatively complex due to its height. At 280 feet tall, a direct load path to the ground is difficult to achieve. Transfer girders are implemented in the design where gravity loads cannot directly reach the foundation through a single column line. Also, the base of the building does not follow the same shape as the upper floors due to a sewer easement. As a result, 19 floors of load plus the roof load are cantilevered out nearly a full bay size from the structure.
FIRE PROTECTION
The construction type is 1B, modified from 1A. The structural frame is rated at 2 hours with spray-on fireproofing applied to all members. The composite floor deck with a 3 ¼” light-weight concrete topping also achieves a fire rating of 2 hours. Fire-rated separations are not required between the various use groups, excluding the third floor. The residential director (RD) apartment, located on the third floor with the fitness area and lounge, is not considered an accessory use since the floor area exceeds the 10% limit of the total floor area. Since the east-facing wall is within thirty feet of the lot line, a one hour fire resistance rating is required. Additionally, due to the cantilever, portions of the north-facing wall also require a one hour fire resistance rating.
Since the building is classified as a high rise, sprinklers, standpipes, fire alarms, and fire detection systems are required. A wet sprinkler system covers the entire building from the ground floor to the stairwell at the roof level. Each sprinkler is designed to cover 225 square feet of floor area. Standpipes are located in each stairwell and extend from the ground floor to the penthouse and roof levels. Fire alarms are also located in all mechanical, electrical, transformer, telephone equipment, and elevator machine rooms. A secondary water supply system is also required due to seismic requirements.
TELECOMMUNICATIONS
For most college students, access to the internet is critical for study. The Tree House provides its students with full coverage throughout the building. Cisco Wireless access points are mounted to the ceiling above the lobby and café on the ground floor. Inside the student health center, there are no wireless access points, likely to mitigate interference with sensitive equipment; however, there is an access point located inside the office space on this floor. On the third floor, there are two access points located in the inner corridor, which provide signal to the surrounding rooms. Similarly, the residential floors have two access points in the hallway which provide signal to the surrounding units. Additionally, each unit is supplied with two cat-6 Ethernet cables located next to the beds. For additional convenience, the laundry room on the third floor features card readers which are connected to a network system allowing students to pay for laundry without coins.
SECURITY
As a college residence, security is an important aspect of design. Closed Circuit Television (CCTV) cameras monitor the entire exterior perimeter of the building as well as all entrances 24 hours. A security desk is also located at the ground floor. Card readers restrict access to various levels and rooms of the building. The first card readers limit access to the ground floor. Once inside the ground floor, students can freely access the lobby and café spaces. Stairs and elevators leading to the student health center on the second floor, community spaces on the third floor, residences on the fourth through the twentieth floor, and the roof and penthouse levels above also require card access. Lastly, each residential unit is also secured by a card reader similar to a hotel. This allows the university to give students, faculty, and maintenance workers specific privileges to various amenities inside the building.
TRANSPORTATION
The requirements for circulation in the building are either met or exceeded throughout the building. On each level of the building a minimum of two exits are required by code. At the ground floor and second floor, three exits are provided. All remaining floors have two exits. The highest occupant load occurs at the ground floor with 216 persons. This load is comfortably handled by the three large doors on this floor with a total 1,132 total exit capacity The maximum exit access travel distance is also well below the 250 ft maximum since the building is only 120 ft long. Two elevators also provide access to all floors of the building except the roof level.
Engineering Systems
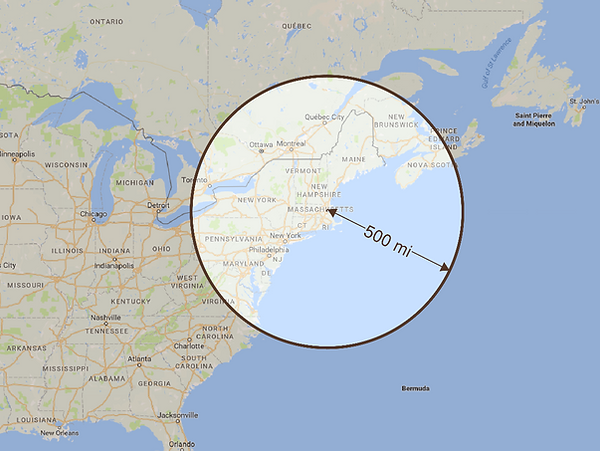
20.79% of the total materials for the project were extracted and manufactured within a 500 mile radius of the site. Procurement of local materials reduces the environmental impact generated during transportation.
BUILDING STATISTICS


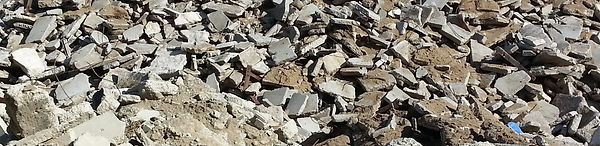
88.80% of the total new wood material cost was certified by the FSC (Forest Steward-ship Council). This certification ensures that wood products are obtained from responsibly managed forests.
Low-flow water closets, lavatories, kitchen sinks, and showers reduce the amount of potable water usage by 33.17% in comparison to a baseline standard according to ADD, Inc.
90.03% of construction waste was recycled and salvaged. In addition, nearly half of the total materials cost was recycled material.

Proposed energy cost usage is 22.83% more efficient than the baseline case according to ASHRAE 90.1-2007. Enhanced commissioning ensures that all systems are operating properly.

General Building Data
Building Name
Location
Occupant Name
Occupancy Type
Size
Height
Number of Stories
Dates of Construction
Total Project Cost
Project Delivery Method
Tree House Residence Hall
578 Huntington Avenue, Boston
Massachusetts College of Art and Design
Residential
145,000 square feet
260 feet
21
June 2010 - June 2012
$64.3m
Single Selection Method
Project Team
Owner
User
Architect
Landscape Architect
Exterior Envelope Consultant
Structural Engineer
MEP/FP & Telecommunications
Civil Engineer
Construction Manager
Geotechnical Engineer
Acoustic Consultant
Code & Accessibility Consultant
Massachusetts State College Building Authority
Massachusetts College of Art and Design
ADD Inc
Ground Inc
Simpson Gumpertz & Heger
Odeh Engineers, Inc
WSP Flack+Kurtz
Nitsch Engineering
Suffolk Construction
Haley & Aldrich Inc.
Cavanaugh Tocci Associates, Inc.
Commercial Construction Consultants - C3
FAÇADE
Inspired by the painting "The Tree of Life" by Gustav Klimt, the building skin is designed to mimic the bark of a tree. 5,500 double-insulated metal panels of various widths and depths are arranged in a pattern that repeats every two floors. Seven custom colors and five gloss levels applied randomly to each panel disguise this repetition. Mimicking a tree reaching toward sunlight, the color gradually becomes lighter along the height of the building. The metal panels are made of aluminum-composite material. The total wall assembly is a pressure-equalized rainscreen system. At the base of the building, an aluminum curtain wall system dominates the western façade. A stone veneer façade also wraps around the base.

Windows also vary in width and depth. In addition, both clear glass and spandrel glass are used in the window assemblies. These windows are low-emission (low-e) and have a low solar heat gain coefficient. Louvers are also applied at various locations to reduce solar heat gain.
The typical window assembly consists of continuous blocking at the sill & head of the rough opening, a continuous air/ vapor membrane lapped at the perimeter with an additional layer across the sill, a window unit with custom head & jamb receptors, AVB counterflashing at the head & jambs, rigid insulation, z-clips, and metal panels with sealant.
GLAZING
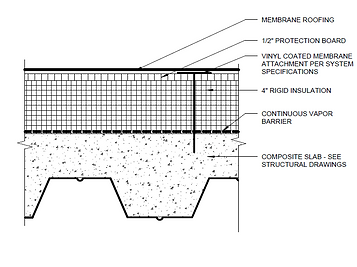

ROOFING
Polyvinyl Chloride (PVC) thermoplastic roofing membrane is applied to all surfaces of the roof. This membrane has integral polyester reinforcement for high strength and durability. Its lighter color gives it a high reflectivity to reduce damage due to excessive heat from exposure to sunlight. Lastly, all seams are heat-weldable to maximize performance over time.
Tree House Biography
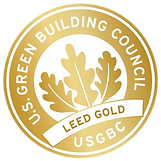
SITE
The majority of the points awarded by LEED to this project came from the design and development of the site. According to data provided by ADD Inc., storm water runoff has been reduced by 33.16% prior to construction of the site. Recharge systems, drywells, and stormceptors also intercept and treat runoff before it reaches natural water bodies. Almost 50% of the site is open space and includes both native and adapted vegetation.
The site was classified as a Brownfield prior to construction. This means that a Licensed Site Professional assessed the site and determined the environmental risks or contaminants to be remediated during construction. Redevelopment and remediation of the site was performed in compliance with the Massachusetts Voluntary Cleanup Program. (More info here)
Automobile pollution is reduced through a fuel-efficient and hybrid vehicle sharing program. The university has also allowed zipcar to use several of their parking spaces on Vancouver Street. Furthermore, the site is conveniently located near six subway stations and several bus stops.
ENERGY
The second highest scoring category is Energy & Atmosphere. Since the building is part of an institution, the designers sought to actively engage the occupants in the sustainable features of the building. Rather than simply automate the windows for optimal performance, the building itself teaches students how to use windows efficiently. A green light is installed on each residential floor. When outdoor temperature is optimal to allow ventilation without increasing load on the mechanical systems, the light is on, and students know to open their windows.